How to Reduce Your Operating Costs During a Cash Crunch
Rising costs in manufacturing can hurt profitability, but strategic cost-saving measures can help. This guide shows how to reduce operating costs by up to 5% and boost productivity, even during a cash crunch.
In today's competitive manufacturing landscape, maintaining profitability amidst rising costs can be a challenge. If your products have become too expensive to manufacture or you're struggling to meet your gross profit targets, you're not alone. But what if I told you that by implementing strategic cost-saving measures, you could reduce your operating costs by 2 to 5%? Imagine minimising waste, optimising labour efficiency, and maximising productivity. In this guide, we'll explore a comprehensive framework for achieving operational excellence and reducing operating costs, even in the midst of a cash crunch.
Before diving into solutions, it's crucial to grasp the magnitude of the cost challenges that manufacturing companies face. Each percentage point of inefficiency can result into significant financial losses.
Whether it's underutilised labour, unnoticed defects, or excessive material waste, the cumulative impact can be staggering. A microscopic leak or a momentary lapse in productivity may appear insignificant, but over time, they can have a long-term impact on profitability and sustainability.
To effectively reduce operating costs, we need to adopt a holistic approach based on the three pillars of operational excellence: People, Profit, and Process.
- People: Engaged employees are the cornerstone of operational success. By fostering a culture of continuous improvement and empowerment, companies can unlock the full potential of their workforce. Ensuring safety, quality, and environmental stewardship lays the foundation for operational excellence.
- Profit: Maximising profitability requires a relentless focus on cost-saving opportunities. From minimising material waste to optimising labour efficiency, every aspect of the production process must be examined for potential savings. The Lean Six Sigma methodologies can provide the framework for systematic improvement.
- Process: Efficiency begins with well-defined processes. By streamlining workflows, eliminating bottlenecks, and embracing innovation, companies can increase productivity while lowering overhead costs. It's not just about achieving short-term gains but cultivating a culture of efficiency and sustainability.
Now that we've established the framework, let's explore actionable strategies for reducing operating costs:
- Labour Optimisation: Analyse staffing levels, skill utilisation, and workflow patterns to identify ways to improve labour efficiency. Implement training programs to enhance skills and empower employees to help with process improvements.
- Waste Reduction: Conduct thorough waste audits to pinpoint areas of excess and inefficiency. Whether it's excess inventory, scrap materials, or energy waste, targeted interventions can yield significant cost savings. Then, implement lean manufacturing principles to minimise waste and maximise value.
- Quality Improvement: Invest in quality control measures to detect and prevent defects before they escalate into costly problems. Implement robust inspection processes, utilise advanced analytics, and foster a culture of accountability to drive continuous improvement in product quality.
- Supplier Collaboration: Form strategic partnerships with suppliers to negotiate favourable terms, streamline supply chains, and cut procurement costs. Explore opportunities for collaborative innovation and value engineering to optimise the cost-value equation.
- Technology Integration: Leverage technology to automate repetitive tasks, enhance process visibility, and improve decision-making. From IoT sensors to predictive analytics, embracing digital transformation can result in increased efficiency and cost savings throughout the manufacturing value chain.
- Energy Efficiency: Implement energy-saving initiatives such as equipment upgrades, process optimisation, and the use of renewable energy to reduce utility costs and reduce environmental impact.
Navigating a cash crunch requires a strategic approach to cost reduction that encompasses people, profit, and process. By fostering a culture of continuous improvement, embracing lean principles, and leveraging technology, manufacturing companies can unlock substantial cost-saving opportunities. Remember that operational excellence is not a destination but a journey—a journey towards sustainable profitability and competitive advantage.
If you're ready to embark on this journey and transform your manufacturing operations, let's connect and explore how we can help you achieve your cost-saving goals. Schedule a Cost Improvement Discovery Mapping Call today. Together, we can transform challenges into opportunities and pave the way for a brighter, more resilient future.
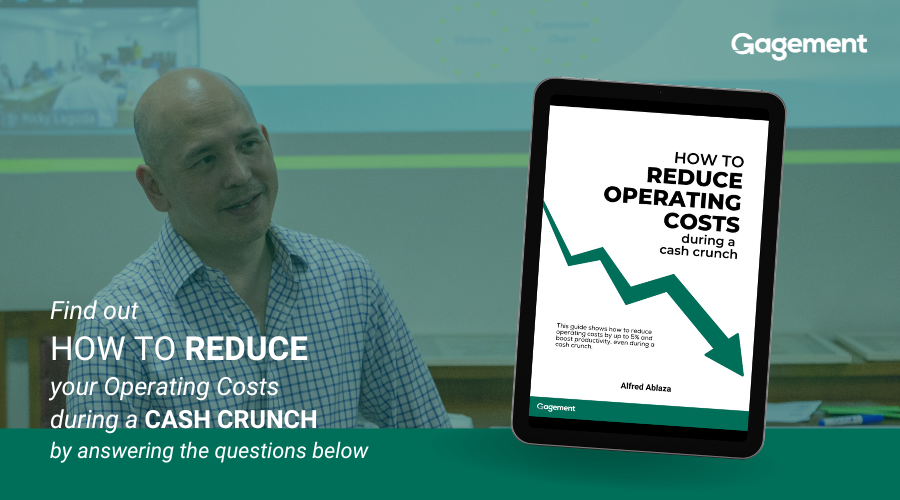
Answer the questions below to get started!